Portable And Fast Inspections
Tubing inspection methods can quickly locate cracks in materials with minimal surface preparation and without the need to contact the material being tested, even if the material in question has complicated geometry.
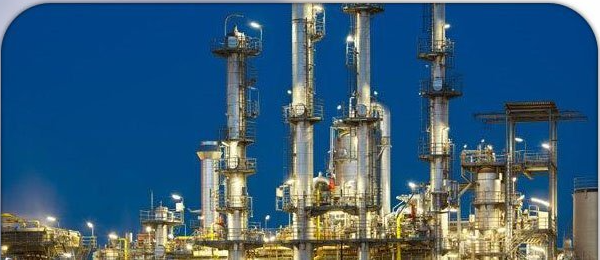

Tubing Inspection
- Eddy Current Tubing Inspection
- Remote Field Tubing Inspection
- IRIS Tubing Inspection
Eddy Current testing uses the principles of electromagnetism as the basis for conducting inspections. When alternating current is applied to a conductor, a magnetic field develops in and around the conductor. When a second conductor is introduced into the magnetic field, an induced current flow is created. Eddy currents are a type of induced current.
In the case of eddy current inspection, eddy currents are created using a probe. Inside the probe is a length of electrical conductor which is formed into a coil. AC flows in the coil at a chosen frequency and a dynamic expanding and collapsing magnetic field forms around the coil as the ac flows through the coil. When electrically conductive material is placed in the coil's magnetic field, electromagnetic induction occurs and eddy currents are induced. These eddy currents flowing in the material generate their own "secondary" magnetic field that opposes the coil's primary magnetic field. The strength of the generated currents, known as the standard depth of penetration vary depending on probe frequency, material conductivity and permeability.
A variety of inspections can be performed
- Crack detection - A primary use of eddy current inspection. Cracks cause a disruption in the circular flow patterns of the eddy currents and weaken their strength.
- Conductivity measurements – Because of the sensitivity to changes in a material's conductive properties and magnetic permeability, eddy current is an excellent tool for material Identification and material sorting.
Multi-frequency eddy current systems available
Multi-frequency eddy current systems refer to equipment that can drive inspection coils at more than two frequencies. This type of instrumentation is used extensively for tubing inspection in power generation and the oil and gas industries.
Major advantages of this inspection are the ability to increase inspection information collected from one probe pull, comparison of same discontinuity signal at different frequencies, mixing of frequencies that helps to reduce or eliminate sources of noise and improves detection, interpretation and sizing capabilities.
The eddy current inspection offers many benefits
- Sensitive to small cracks and defects
- Detects surface and near-surface defects
- Immediate results are available
- Equipment is portable
- Minimum part preparation is required
- Probes do not need to contact the part
- Ability to inspect complex shapes and sizes